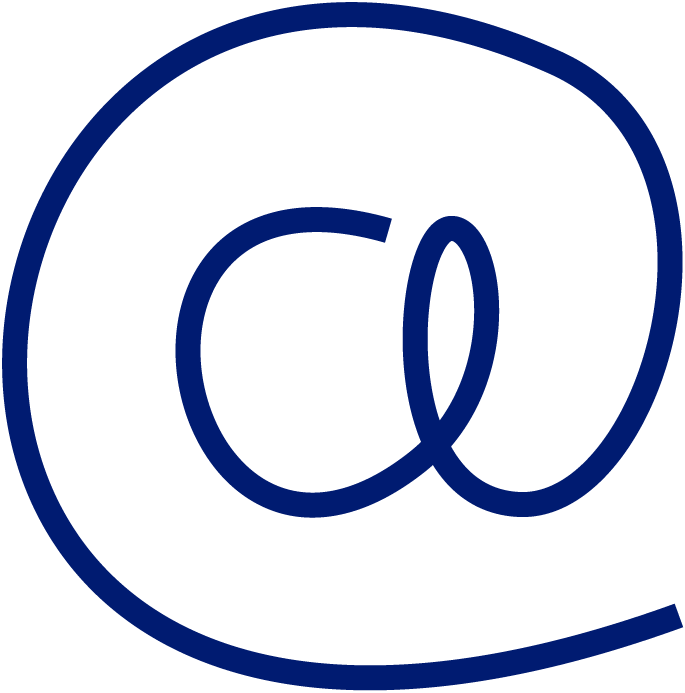
Reducing the Total Cost of Ownership (TCO) is the only way to make real savings or do more with the same resources and budget, without compromising the effectiveness and quality of your learning projects.
Do you really know the whole costs generated by your training projects? With a TCO analysis, you assess all the costs of your training project - direct and indirect costs. Thus you can make the right decisions.
Here is an overview of the TCO approach and main cost items impacting learning projects. It will change the way you consider your projects and will boost the productivity of your L&D organisation!
The TCO explained in a 5-minute video
The secret to effectively calculate the TCO of your training projects
The main key success factor to effectively calculate the TCO of your training projects is to work as a team.
Set up a cross-functional team involving representatives familiar with the costs at different levels: purchasing, design teams, training teams and a financial person to assess the internal costs and confirm the savings.
6 costs to assess when working out the TCO of a training project
TCO includes both expenditure items and items that use internal resources.
1. Upstream costs:
Essentially, the internal costs generated by the tender costs and the time spent aligning the various stakeholders
2. Implementation costs:
Your initial outlay on creating and validating your project. It’s interesting to balance this investment with the project expected lifetime, the number of trainees and of course the project’s stakes
3. Acquisition costs:
The recurring costs that you pay for each session such as Trainers’ cost, material, administration costs, Travel & Accommodations etc. The total increases with the volume.
4. The cost of use:
It varies with the actual duration of the project. Quality, fill-rate, training update will impact this cost item. The duration of a well-structured project that meets the initial estimates will enable you to amortize the implementation costs. Conversely, a training course that doesn't go well will generate re-engineering costs. You may even have to re-invest in creating a new module.
5. The management costs:
It is generated by the time your teams spend to obtain the expected level of service from suppliers or the team in charge of training delivery. This should be a long standing investment.
6. The costs of destruction and recycling:
Mainly generated by managing the catalogue in the systems.
Identify the cost drivers
Once the cost items have been identified, you can identify the cost drivers (the factors that make costs vary).
At this point, you need to question these items and their legitimacy in comparison to the project's overall goals:
- Will we really optimise TCO or simply transfer the cost?
- Will we generate new costs to offset the unsatisfied goals?
Leverage the most appropriate productivity factors
There are three sources of productivity you should be aiming for:
- QUICK WINS: gains that you can obtain immediately without any impact on quality or on your goals
- RECURRING TASKS, which can be standardised and optimised to free up resources in the future
- MAJOR COST ITEMS, which can be optimised without compromising your goals
The aim is to draw up concrete action plans.
This post was written by Anne Fessan when she was responsible for International L&D projects at Cegos France